Working Principle
A typical configuration of a column is shown above. It consists two main sections which are washing section and recovery section. In the section below the feed point(the recovery section),particles suspended in the descending water phase contact a rising swarm of air bubbles produced by lance-type bubble generators in the column base. Floatable particles collide with and adhere to the bubbles and are transported to the washing section above the feed point. Non-floatable material is removed through tailing valve installed in high-level. Gangue particles that are loosely attached to bubbles or are entrained in bubble slipstreams are washed back under the effect of froth washing water, hence reducing contamination of the concentrate. The wash water also serves to suppress the flow of feed slurry up the column towards the concentrate outlet. There is a downward liquid flow in all parts of the column preventing bulk flow of feed material into the concentrate.
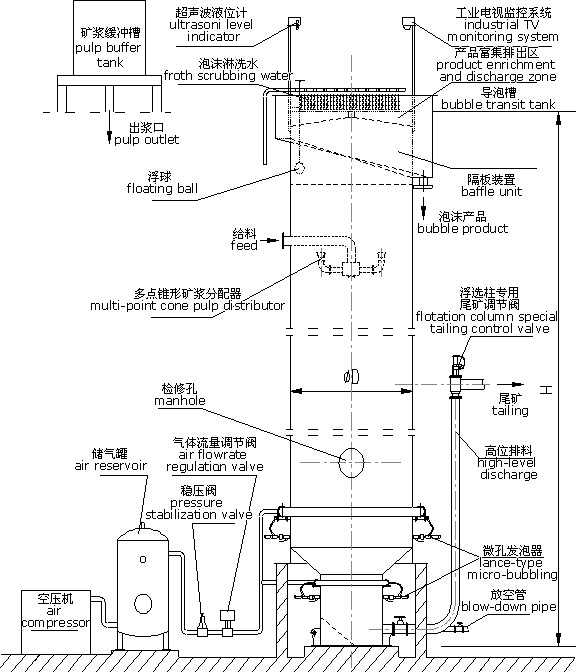
Features
- High concentrate ratio;
Compared with the conventional flotation cell, flotation column has rather high foam layer, which can enhance the concentration function for target minerals, thus to producer higher assay concentrate.
- Low power consumption;
Without any mechanical propeller or agitator, this equipment realizes the froth flotation by bubbles generated from air compressor. In general, column call has 30% lower power consumption than flotation machine.
- Low construction cost;
Only small footprint and easy foundation needed to install flotation column.
- Low maintenance;
The parts in flotation column are tough and durable, only sparger and valves are recommended to be replaced regularly. Furthermore, the maintenance can be operated without shutdown the equipment.
- Automatic control.
Equipped with automatic control system, the operators can operate flotation column only by click the computer’s mouse.
Applications
Flotation column can be used to deal with nonferrous metals such as Cu, Pb, Zn ,Mo, W minerals, and non-metallic minerals such as C, P, S minerals, as well as waste liquids and residues of chemical industry, paper making, environmental protection and so on, especially used in technical innovation of old mining companies and capacity expansion to achieve " greater, faster, better and more economical " performance .
Equipment Parts
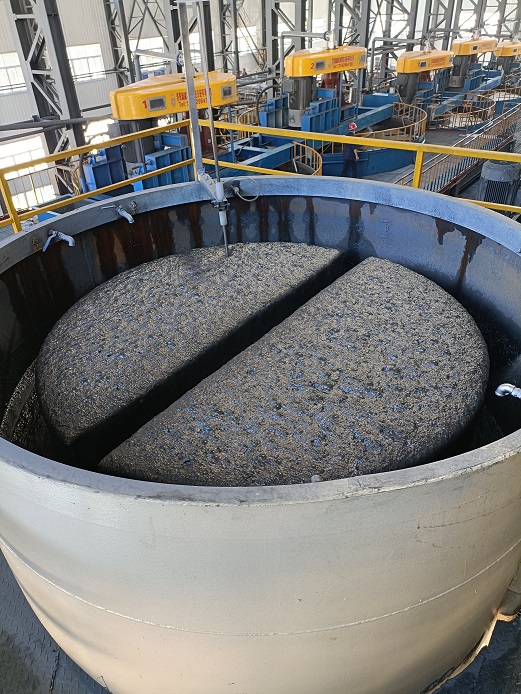
Foam Trough
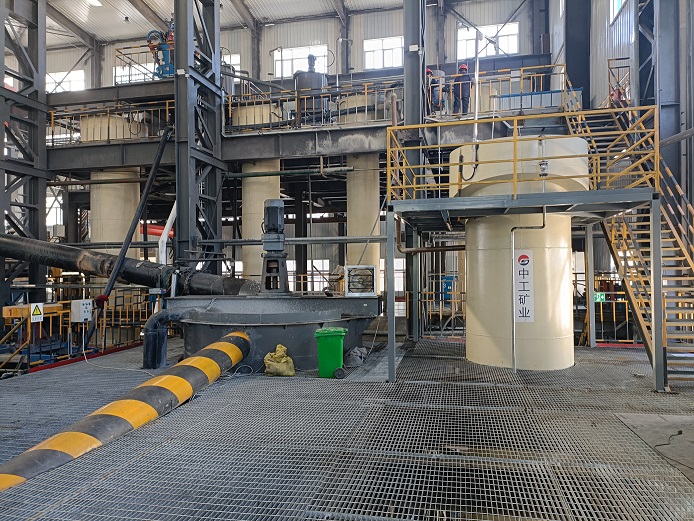
Platform and Column cell tank
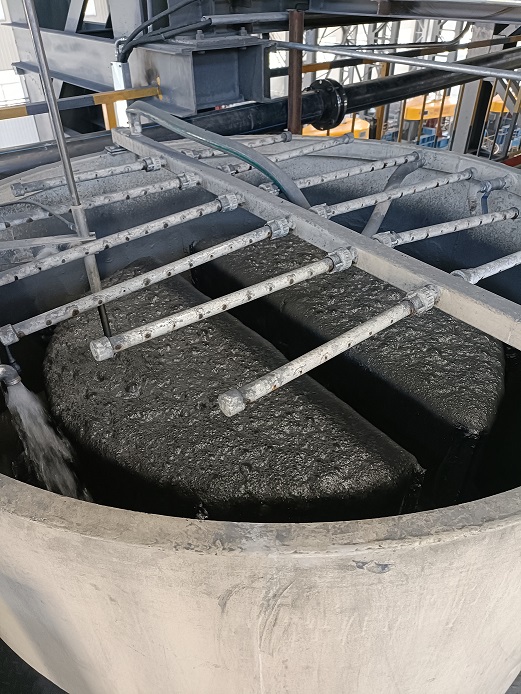
Tailing Valve
Parameters
Specification ΦD×H(m) |
Bubble Zone Area m2 |
Feed concentration % |
Capacity m3/h |
Aeration rate m3/h |
ZGF Φ0.4 ×(8~12) |
0.126 |
10-50 |
2-10 |
8-12 |
ZGF Φ0.6 ×(8~12) |
0.283 |
10-50 |
3-11 |
17-25 |
ZGF Φ0.7 ×(8~12) |
0.385 |
10-50 |
4-13 |
23-35 |
ZGF Φ0.8 ×(8~12) |
0.503 |
10-50 |
5-18 |
30-45 |
ZGF Φ0.9 ×(8~12) |
0.635 |
10-50 |
7-25 |
38-57 |
ZGF Φ1.0 ×(8~12) |
0.785 |
10-50 |
8-28 |
47-71 |
ZGF Φ1.2 ×(8~12) |
1.131 |
10-50 |
12-41 |
68-102 |
ZGF Φ1.5 ×(8~12) |
1.767 |
10-50 |
19-64 |
106-159 |
ZGF Φ1.8 ×(8~12) |
2.543 |
10-50 |
27-92 |
153-229 |
ZGF Φ2.0 ×(8~12) |
3.142 |
10-50 |
34-113 |
189-283 |
ZGF Φ2.2 ×(8~12) |
3.801 |
10-50 |
41-137 |
228-342 |
ZGF Φ2.5 ×(8~12) |
4.524 |
10-50 |
49-163 |
271-407 |
ZGF Φ3.0 ×(8~12) |
7.065 |
10-50 |
75-235 |
417-588 |
ZGF Φ3.2 ×(8~12) |
8.038 |
10-50 |
82-256 |
455-640 |
ZGF Φ3.6×(8~12) |
10.174 |
10-50 |
105-335 |
583-876 |
ZGF Φ3.8 ×(8~12) |
11.335 |
10-50 |
122-408 |
680-1021 |
ZGF Φ4.0 ×(8~12) |
12.560 |
10-50 |
140-456 |
778-1176 |
ZGF Φ4.5 ×(8~12) |
15.896 |
10-50 |
176-562 |
978-1405 |
ZGF Φ5.0 ×(8~12) |
19.625 |
10-50 |
225-692 |
1285-1746 |
FAQ
1.What are your prices?
Our prices are subject to model.
2.Can you supply the relevant documentation?
Yes, we can provide most documentation including Certificates of Analysis / Conformance; Insurance; Origin, and other export documents where required.
3.What is the average lead time?
The average lead time would be 3 months after advance payment.
4.What kinds of payment methods do you accept?
Negotiable.